Скоро!
Событий нет.
|
 |
29 августа 2007
Пайка в паровой фазе
Введение
Среди известных методов пайки поверхностно монтируемых электронных компонентов (ЭК) на печатную плату (ПП) в настоящее время наиболее распространена пайка оплавлением. Данный метод реализуется на практике с помощью различных вариантов, среди которых, в свою очередь, широко применяется пайка в печи оплавления с применением ИК-нагрева, естественной либо принудительной конвекции, а также их комбинаций. Следует отметить, что применение ИК-метода из-за сложностей в обеспечении равномерности нагрева в настоящее время потерял свою популярность. Подробно эти способы пайки, их достоинства, недостатки и особенности создания термопрофилей рассмотрены в статье «Режимы пайки оплавлением».
Помимо вышеуказанных способов, ограниченное применение находит ряд перечисленных ниже:
- пайка в паровой фазе (vapor phase reflow, VPS);
- кондукционная пайка (hot bar soldering);
- лазерная пайка (laser soldering).
В данной статье рассмотрена пайка в паровой фазе (другие названия: конденсационная пайка, пайка с конденсацией насыщенного пара – condensation reflow, saturated vapor soldering).
Данная технология была запатентована в 1975 году Фалем и Амманнином (C. Pfahl и H.H. Ammannin), получила распространение в середине 70-х г.г., а в 80-е ее можно было считать одной из доминирующих технологий пайки. Тем не менее, к началу 90-х ее использование для пайки электронных компонентов практически сошло на нет, как из-за проблем самой технологии (наличия высокого уровня дефектов, прежде всего капиллярного затекания припоя из-за разных скоростей нагрева выводов и КП, что усугублялось проблемами с копланарностью и приводило к образованию непропаев, а также появления дефекта надгробного камня и растрескивания корпусов ЭК), так и произошедших значительных усовершенствований технологии оплавления с применением ИК-нагрева. Появившиеся впоследствии системы с преобладанием принудительной конвекции обеспечивали эффективный нагрев при отсутствии специфических проблем технологии пайки в паровой фазе. Значительных нововведений в технологии пайки в паровой фазе не наблюдалось вплоть до настоящего времени.
Тем не менее, в последнее время данная технология переживает период нового подъема. Ряд новых технических решений позволил в значительной степени устранить прошлые недостатки, после чего на передний план вышли несомненные достоинства процесса пайки в паровой фазе: равномерный нагрев сборки, принципиальная невозможность ее перегрева, осуществление пайки в полностью инертной среде, отсутствие сложной процедуры создания термопрофилей.
В данной статье мы рассмотрим ключевые особенности процесса, варианты его реализации, оборудование и дополнительные возможности, предоставляемые данной технологией.
Особенности процесса
Предшествующие пайке операции – нанесение паяльной пасты и установка компонентов – выполняются аналогично техпроцессу с применением пайки оплавлением в конвекционной печи. Дополнительных требований к этим операциям пайка в паровой фазе не предъявляет.
Основа процесса пайки в паровой фазе – конденсация паров специальной нагретой жидкости на печатной плате, в результате которой энергия, выделяемая при фазовом переходе, передается открытым участкам сборки. При этом происходит оплавление припойной пасты и образование паяных соединений. Температура кипения жидкости – равновесная (она же максимальная) температура, обеспечиваемая данным видом пайки. Выбирается жидкость с известной точкой кипения, равной требуемой температуре пайки, после нее конденсация пара на сборке прекращается и дальнейший рост температуры физически невозможен. Вследствие этого устраняется необходимость точного подбора и строгого контроля максимальной температуры и становится принципиально невозможным перегрев сборки [7, 8].
В качестве рабочей жидкости используются химически инертные, некоррозионные составы на основе фтороуглерода (преимущественно применяются перфторполиэфирные (PFPE, Perfluoropolyether) жидкости GALDEN), имеющие различные точки кипения; для пайки электронных модулей применяются жидкости с типичным диапазоном точек кипения от 200°С до 260°С и выше (вплоть до 320°С). Жидкости не содержат фреон и не наносят ущерба окружающей среде. Некоторые системы пайки позволяют смешивать две жидкости, получая смесь с третьим значением точки кипения.
В процессе развития технологии сформировались два варианта ее реализации: пайка насыщенным и ненасыщенным паром. Первый вариант находит применение в т. н. вертикальных системах с резервуаром («vertical tank») и вертикальным движением сборки при пайке, второй – в горизонтальных, оснащенных рабочей камерой («vapor chamber») и горизонтальным движением сборки. Ряд производителей работает с насыщенным паром (ASSCON Systemtechnik-Elektronik GmbH), другие – с ненасыщенным (rehm Anlagenbau GmbH). Ниже рассмотрены особенности реализации каждого варианта, их достоинства и недостатки.
Пайка насыщенным паром. Вертикальные системы
Метод основан на передаче тепла сборке от сконденсированной на ней жидкости. Типичная последовательность выполнения операции пайки при этом следующая (рис. 1):
- Сборка перемещается в резервуар и располагается над зоной пара, образующегося над нагретой до точки кипения рабочей жидкостью. Осуществляется предварительный нагрев сборки (ИК-нагревом, предварительным погружением в паровую среду и прочими методами). Методы предварительного нагрева подробно рассмотрены ниже.
- Сборка погружается в паровую среду и нагревается. Воздух вытесняется инертным фторуглеродным паром, так как вес паров жидкости высок, и дальнейшие процессы происходят в полностью инертной среде. Паровой защитный покров полностью накрывает сборку.
- Пар конденсируется на поверхности сборки и передает ей свою энергию. Образуется защитная инертная атмосфера без необходимости использования азота.
- Сборка нагревается до температуры насыщенного пара, после чего нагрев прекращается независимо от того, сколько времени сборка проведет в паровой зоне. Время достижения температуры пайки – обычно от 5–6 сек. до 50 сек. для больших сборок. Происходит непосредственный процесс пайки.
- После выхода сборки из паровой области на ней еще остается сконденсировавшаяся жидкость. Благодаря остающейся внутренней теплоте сборки, она испаряется, и сухая плата покидает рабочую зону. Остатков жидкости на плате не образуется.
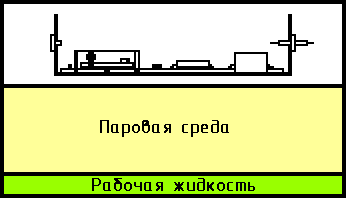
a)
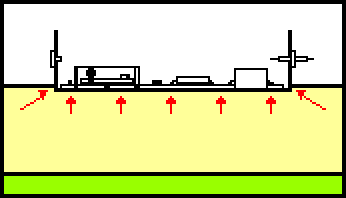
б)
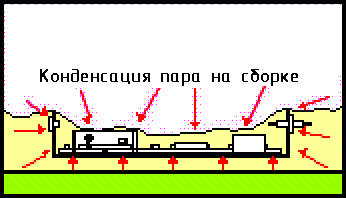
в)
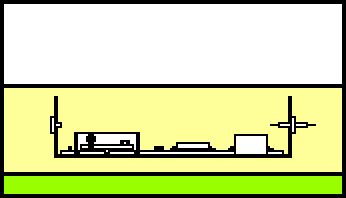
г)
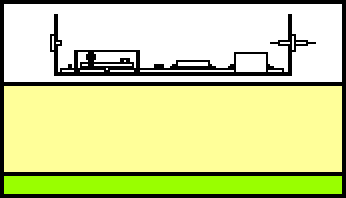
д)
Рис. 1. Последовательность выполнения операции пайки насыщенным паром (вертикальные системы). Рисунок из [19]
Рекомендуемые установки температуры: для эвтектических припоев – 200°С, для бессвинцовых (как, например, SnAg3,5 с точкой плавления 221°C) – 230°С [18].
Пайка ненасыщенным паром. Горизонтальные системы
Технология применения ненасыщенного пара основана на принципе инжекции.
Сборка перемещается с помощью горизонтального конвейера в рабочую камеру, которая затем герметизируется. Нижняя и боковые стенки камеры содержат нагревательные элементы, температура нагрева которых может быть задана программно. Далее происходит впрыск заданного объема рабочей жидкости в рабочую камеру. При контакте жидкости с поверхностью стенок камеры, жидкость вскипает и образует паровое облако (рис. 3). Скорость нагрева для каждой конкретной сборки может контролироваться и изменяться в зависимости от объема впрыскиваемой жидкости. Откачанный после окончания процесса пайки пар реконденсируется, очищается с целью удаления из него флюса и возвращается в бак-хранилище [4]. Время цикла процесса пайки в горизонтальной системе сходно с таковым для пайки оплавлением в конвекционной печи.
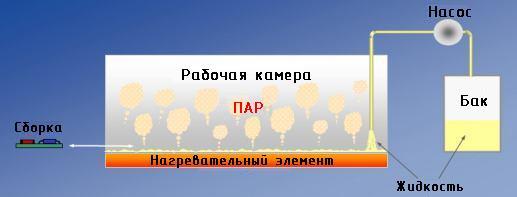
Рис. 2. Схема процесса пайки в паровой фазе с применением инжекции. Рисунок из [13]
Как было отмечено выше, количество образующегося пара, а, следовательно, и его теплоемкость, может управляться изменением количества впрыскиваемой рабочей жидкости. Для горизонтальных систем на характер термопрофиля оказывают воздействие несколько параметров, среди которых можно выделить основные:
- количество впрыскиваемой жидкости;
- время выдержки после впрыска;
- степень откачки пара;
- охлаждение.
Процесс пайки включает несколько стадий впрыска/откачки, связанные с необходимостью предварительного нагрева сборки (см. ниже). Для систем пайки rehm Anlagenbau GmbH [14] производитель выделяет 13 стадий процесса:
- Впрыск 1.
- Выдержка.
- Впрыск 2.
- Выдержка.
- Откачка.
- Выдержка.
- Впрыск 3.
- Выдержка.
- Впрыск 4.
- Выдержка.
- Тонкая откачка.
- Грубая откачка.
- Охлаждение.
Система может быть легко интегрирована в автоматизированную линию и таким образом адаптирована для больших объемов производства. Сборка, перемещающаяся по конвейеру, проходит три зоны: входную, рабочую и зону охлаждения (рис. 3).
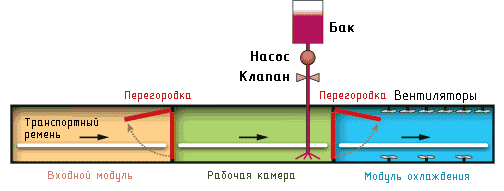
Рис. 3. Конвейерная схема горизонтальной системы пайки в паровой фазе. Рисунок из [4]
Основные проблемы пайки в паровой фазе
Одной из основных трудностей при реализации пайки в паровой фазе является сложность управления скоростью подъема температуры в момент конденсации пара на поверхности сборки, так как процесс этот происходит очень быстро. Данный механизм передачи тепла характеризуется очень высокой эффективностью – коэффициент теплопередачи для него составляет ≈ 300 Вт/(м²∙K), в то время как для принудительной конвекции (в воздушной или инертной атмосфере) его значение на порядок меньше.
Вследствие этого значения скорости подъема температуры при пайке в паровой фазе могут достигать 25 – 40°С/сек. (бо́льшие значения характерны для небольших по размерам компонентов), что потенциально может вызвать появление таких дефектов, как растрескивание керамических чип-компонентов, смещение компонентов, эффект «надгробного камня», капиллярное затекание припоя. С развитием технологии пайки в паровой фазе появился ряд способов, позволяющих установить контроль над этой скоростью.
Предварительный нагрев сборок помогает обеспечить более плавный переход к температуре оплавления. В установках пайки в паровой фазе применяются как традиционные методы предварительного нагрева (ИК-нагрев, естественная и принудительная конвекция), так и нагрев средствами самой паровой фазы.
Так, компания R&D Technical Services, Inc. применяет в ряде своих систем нагрев с помощью принудительной конвекции (4 зоны нагрева) [23].
В ряде вертикальных систем управление скоростью нагрева идет за счет последовательного погружения сборки в паровую среду, чем регулируется объем конденсирующегося на сборке пара (рис. 4).
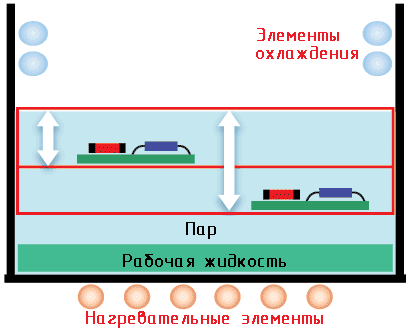
Рис. 4. Схема предварительного нагрева вертикальной системы пайки в паровой фазе. Управление скоростью нагрева идет за счет последовательного погружения сборки в паровую среду. Красным очерчен доступный объем пара для каждой глубины погружения сборки. Рисунок из [4]
Например, технология «мягкой» паровой фазы (Soft Vapor Phase, SVP) от компании IBL-Löttechnik позволяет добиваться различных скоростей нагрева сборки, программируя соответствующие режимы ([20] и рис. 5). В сочетании с включенным предварительным ИК-нагревом, данная технология обеспечивает формирование популярных термопрофилей в форме плато (рис. 6), где ИК-нагрев линейно поднимает температуру сборки, а включение «мягкого» режима паровой фазы задает форму кривой с выдержкой и дальнейшим плавным ростом температуры. Подобная технология, названная «контроль температурных градиентов» (temperature-gradient-control, TGC), предлагается компанией ASSCON Systemtechnik-Elektronik GmbH [12].
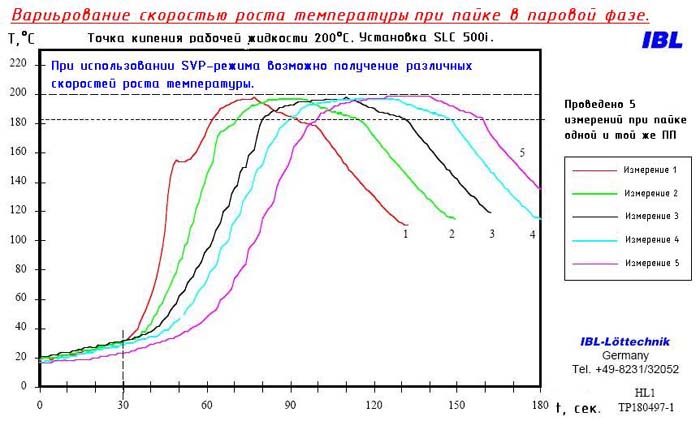
Рис. 5. С использованием технологии SVP можно точно контролировать и изменять скорость нагрева сборки. Рисунок из [20]
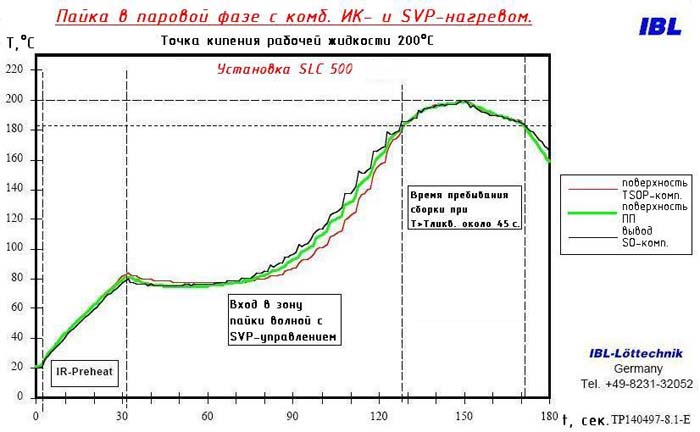
Рис. 6. Сочетание предварительного ИК-нагрева и технологии SVP позволяет формировать термопрофили в форме плато. Рисунок из [20]
Даже без включения ИК-нагрева при нагреве сборки исключительно средствами паровой фазы можно добиться плавного подъема температуры (на рис. 7 – со скоростью, немного превышающей 2°С/сек). Гибко настраивая режимы нагрева, в режиме SVP можно чередовать быстрый и плавный нагрев средствами паровой фазы (рис. 8).
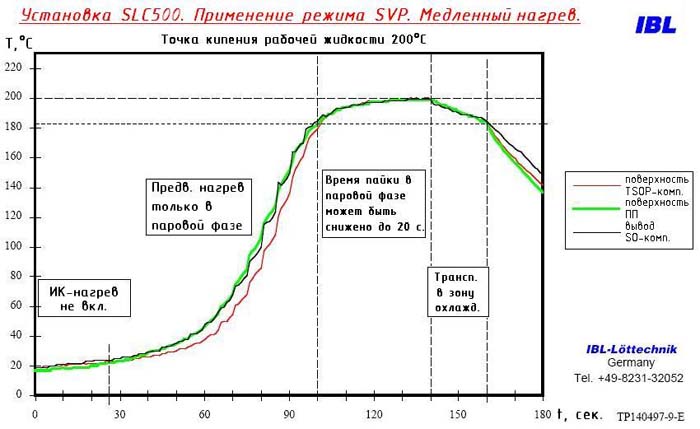
Рис. 7. Обеспечение плавного подъема температуры без включения ИК-нагрева с помощью технологии SVP. Рисунок из [20]
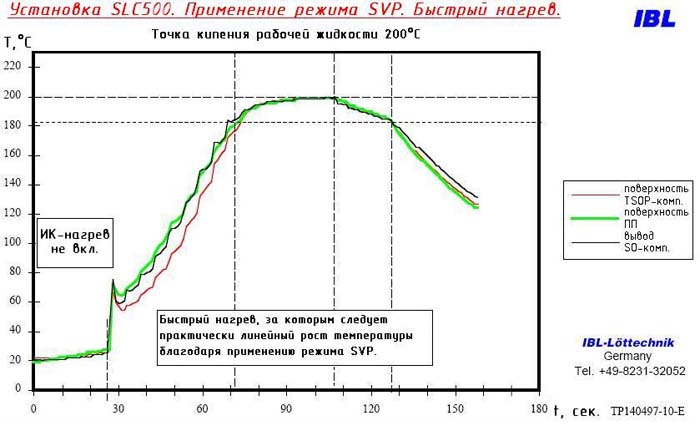
Рис. 8. Чередование быстрого и плавного нагрева без включения ИК с помощью технологии SVP. Рисунок из [20]
Системы оплавления построенные по таким технологиям, включают дополнительные зоны предварительного инфракрасного либо конвекционного нагрева непосредственно перед рабочим резервуаром пайки в паровой фазе. Пример вертикальной системы, встроенной в автоматизированную линию и оснащенной устройствами загрузки/выгрузки, конвейером для транспортировки сборок, камерами предварительного нагрева и охлаждения, представлен на рис. 9.
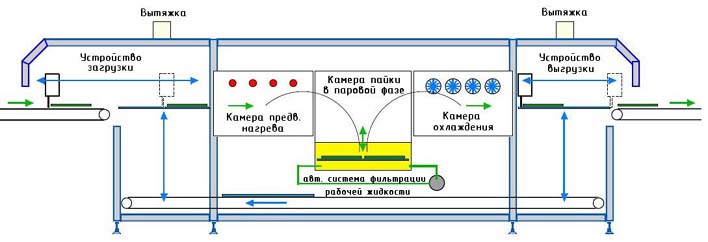
Рис. 9. Вертикальная система, встроенная в автоматизированную линию и оснащенная камерой предварительного нагрева. Рисунок из [22]
Таким образом, термопрофилирование при пайке в паровой фазе включает установку параметров предварительного нагрева, скорости движения конвейера, времени выдержки в рабочей зоне. Как и для традиционных печей оплавления, пайка в паровой фазе требует индивидуального профиля оплавления для каждой новой сборки, однако, термопрофилирование значительно упрощается, так как максимальная температура рабочей жидкости жестко фиксирована. Все требования, относящиеся к обеспечению предварительного нагрева в ИК-системах, справедливы и для соответствующих зон пайки в паровой фазе [1]. Пример типового профиля оплавления представлен на рис. 10.
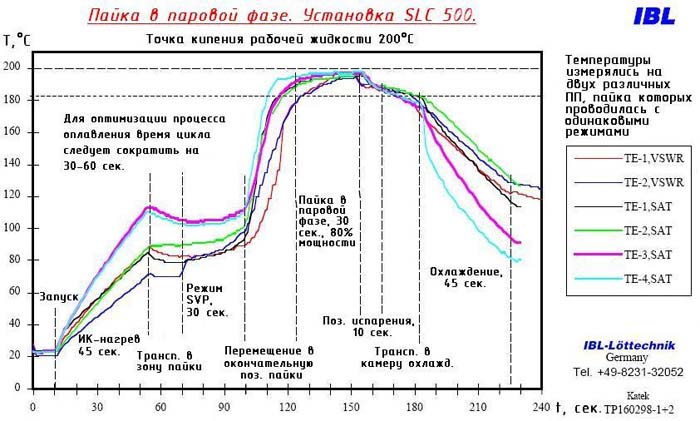
Рис. 10. Типовой профиль оплавления для пайки в паровой фазе. Рисунок из [20]
В горизонтальных системах, как уже было сказано выше, управление скоростью нагрева ведется с помощью изменения объема впрыскиваемой рабочей жидкости, который пропорционален количеству пара в рабочей камере (рис. 11). Применяется ступенчатый, многоэтапный впрыск. Уменьшение скорости нагрева и построение различных термопрофилей (линейного, седлообразного) также может быть достигнуто удалением во время операции части пара из камеры с помощью вакуумного насоса. Скорость откачки пара после пайки программируется, чем обеспечивается требуемый диапазон скоростей охлаждения (обычно в пределах 2 – 3°C/сек.) [4].
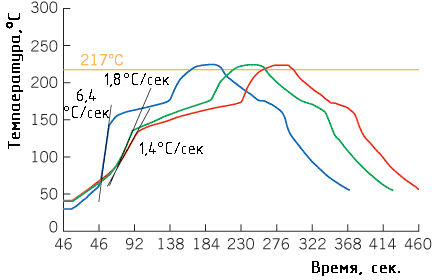
Рис. 11. Влияние на температурный профиль объема впрыскиваемой жидкости при T = 230°С для горизонтальной системы. Рисунок из [4]
Сравнение систем пайки насыщенным и ненасыщенным паром
По сравнению с пайкой ненасыщенным паром, пайка в атмосфере насыщенного предоставляет ряд преимуществ (по данным [10]):
- Вертикальная система отличается большей равномерностью передачи тепла. Так как ненасыщенный пар представляет собой смесь частиц пара и кислорода (либо инертного газа с кислородными включениями), равномерность теплопередачи обеспечить довольно сложно. Возможно образование на ПП зон с нестабильной теплопередачей, что может привести к неполному оплавлению паяльной пасты. Как пайка, так и предварительный нагрев идут с влиянием конвекции, что делает теплопередачу менее эффективной и более бурной. Также негативно влияет на равномерность поддержания температуры большое количество этапов процесса в системах с ненасыщенным паром.
- Также в случае ненасыщенного пара отсутствует реальная бескислородная атмосфера, так как в нем обязательно присутствуют частицы кислорода, хотя бы в небольшом количестве. При пайке может использоваться защитная азотная атмосфера.
- Для горизонтальной системы требуется дополнительный нагрев стенок рабочей камеры, тогда как в вертикальном резервуаре нагревается только его дно, а стенки остаются холодными. В первом случае отложения флюса на стенках камеры могут подвергнуться воздействию высоких температур, разрушению молекулярной структуры и испарению. Эти пары могут выступить в качестве загрязнений паяных соединений сборки. В вертикальной системе это невозможно.
- Горизонтальную систему отличает более длинный цикл пайки, включающий неоднократно повторяющиеся этапы инжекции рабочей жидкости в камеру, выдержки и выпуска (до 13 этапов). Производители таких систем предупреждают о возможном перегреве сборки при неправильной настройке параметров процесса [10, 17].
- Система с насыщенным паром требует меньших расходов как на приобретение оборудования, так и на его эксплуатацию, так как отсутствует необходимость в системе инжекции, помпах откачки и их обслуживании, затратах на реконденсацию рабочей жидкости. При работе вертикальная система затрачивает меньшее количество энергии, в частности, по причине отсутствия многочисленных циклов впуска/откачки нагретой рабочей среды. В вертикальных системах вся затраченная энергия идет непосредственно на однократное создание паровой среды вокруг паяемой сборки.
- Малое количество настроечных параметров – фактически, настраивается только скорость роста температуры при нагреве, что обеспечивает более надежный контроль температур в процессе оплавления.
С другой стороны, у вертикальных систем также присутствует ряд недостатков, основные из которых перечислены ниже (по данным [4]):
- Более сложное встраивание вертикальной системы в автоматизированную линию, так как ПП в процессе пайки перемещается в вертикальном направлении.
- Более сложная реализация вакуумной системы для устранения пустот в паяных соединениях (см. ниже). В горизонтальной системе естественной вакуумной камерой служит рабочая камера. В вертикальной системе необходимо ее дополнительное обустройство, так как рабочий резервуар во время процесса заполнен рабочей жидкостью и ее паром, которые не подлежат откачке. Перемещение сборки с оплавленным припоем до его кристаллизации нежелательно.
- Предварительный нагрев сборок методом погружения в паровую среду, применяемый в вертикальных системах, может вызвать турбулентность потоков пара рабочей жидкости и частичное смешивание его с окружающей атмосферой. Следствием этого может стать, с одной стороны, непредсказуемый объем сконденсированного пара, с другой – возможное изменение его температуры.
- Нежелательным является возвратно-поступательное движение сборки при предварительном нагреве, которое осуществляется в вертикальных системах.
- Бо́льшие потери рабочей жидкости, связанные с ее испарением с поверхности сборки после пайки (порядка 25–50 г/ч [12]). У горизонтальных систем, построенных по замкнутому циклу, такие потери весьма незначительны, и составляют около 1 – 1,5 г/цикл [4].
Основные достоинства пайки в паровой фазе
На основании вышесказанного, приведем основные достоинства, отличающие метод пайки в паровой фазе в целом [1, 4, 6, 10, 18]:
- Невозможен перегрев сборки свыше заранее известной температуры конденсации пара.
- Относительно простой процесс термопрофилирования. Метод особенно пригоден для многономенклатурного мелкосерийного производства, так как не требуется трудоемкий подбор профилей в зависимости от конструкции сборки.
- Равномерное распределение температур по поверхности сборки и быстрый нагрев даже при большой разнице в теплоемкости различных компонентов и областей ПП. Нет необходимости в выдержке для обеспечения равномерного нагрева. Отсутствие эффектов затенения и зависимости нагрева от цвета и характера поверхности компонентов. Особенно пригоден для больших и массивных сборок, а также для изделий, включающих компоненты сложной формы.
- Химические основы процесса обеспечивают 100%-инертную атмосферу при пайке. Отсутствие окисления при предварительном нагреве (средствами паровой фазы) и пайке. Применяемый флюс, таким образом, может обладать умеренной активностью.
- Хорошая повторяемость результатов процесса.
- Надежная пайка всех ЭК сборки, включая BGA, CSP и пр.
- Простой переход от эвтектической к бессвинцовой пайке (пример профиля для бессвинцовой пайки см. на рис. 12). Достаточно простая пайка смешанных сборок при наличии ЭК как с традиционным, так и бессвинцовым покрытием выводов.
- Так как максимальная температура процесса невелика (как правило, 200°С – для эвтектической пайки, 230°С – для бессвинцовой), минимизируется вероятность эффекта «попкорна».
- По данным R&D Technical Service [24], внутренняя температура корпусов ЭК на 20–30 °С ниже температуры выводов; термосимметрия (зависимость температуры на ПП от ее расположения/направления потока теплоносителя) – менее 5°С; чувствительность к нагрузке (колебания температуры при прохождении сборки через зону нагрева) – менее 2°С; повторяемость процесса оплавления (изменение температуры оплавления в печи с течением времени, измеренное на уровне ПП) – 1–4°С.
- Отсутствие расслоения ПП. Возможность применения процесса для изделий на гибких и многослойных платах.
- Дружественность процесса по отношению к окружающей среде – менее агрессивные пары флюса, чем в других техпроцессах.
- Низкие затраты на операцию, малое энергопотребление (обычно 5-12 кВт).
- Переданная сборке тепловая энергия линейно зависит от подведенной энергии нагрева – упрощение контроля процесса.
- Относительная простота выполнения и отсутствие частой необходимости технического обслуживания.
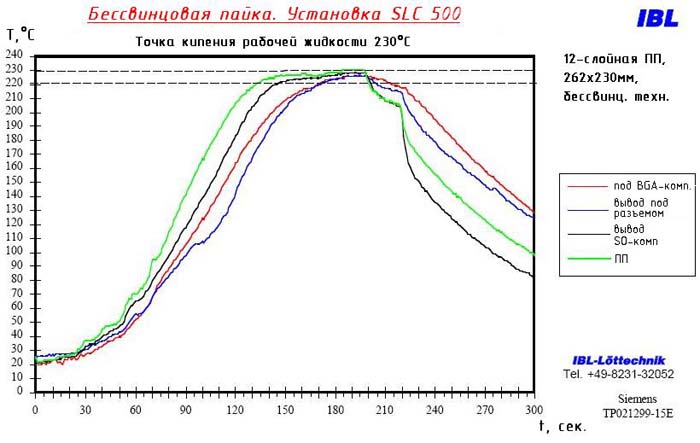
Рис. 12. Пример профиля оплавления для бессвинцовой пайки в паровой фазе. Рисунок из [20]
Оборудование
На рынке представлен широкий спектр моделей: как одиночных, для единичного и мелкосерийного производства (рис. 13), так и встраиваемых в линию систем пайки для больших объемов выпуска (рис. 14).
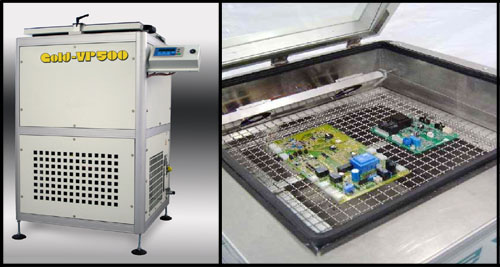
Рис. 13. Одиночная система пайки в паровой фазе для единичного и мелкосерийного производства. Модель VP-500 Gold. Фото из [2]
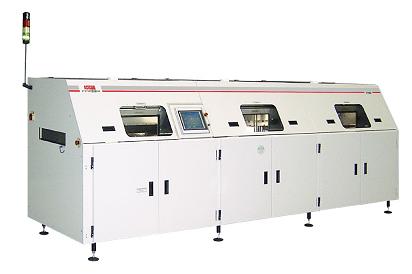
Рис. 14. Автоматизированная встраиваемая в линию система пайки в паровой фазе для больших объемов выпуска. Модель VP 2000. Фото ASSCON Systemtechnik-Elektronik GmbH
Основные параметры оборудования включают в себя следующие (в скобках даны типовые значения для встраиваемых в линию систем по данным [12, 15, 16, 23]):
- одиночный либо двойной конвейер;
- минимальные и максимальные габариты ПП (от 50х50 до 650х650 мм);
- максимальную высоту сборки, измеряемую от поверхности ПП в обе стороны (20/20, 30/10, 45/20, 55/20 мм вверх/вниз);
- требуемая ширина свободной от установки ЭК зоны на ПП (3–5 мм);
- максимальная мощность (12 – 18 кВт);
- средняя потребляемая мощность (при полной загрузке – 7 кВт и в режиме ожидания – 4 КВт);
- метод обеспечения предварительного нагрева, количество зон (до 4-х);
- диапазон рабочих температур пайки (200–320°С в зависимости от используемой рабочей жидкости);
- средний расход рабочей жидкости (25–50 г/ч для вертикальных систем);
- емкость резервуара (20–50 л) либо максимальный вес рабочей жидкости (15–40 кг);
- время выхода на рабочий режим (30 мин);
- среднее время цикла (5 мин).
Во многих моделях оборудования возможно непосредственно наблюдать за процессом пайки через смотровое окно.
Применение вакуума при пайке
Многие производители оборудования представили технологии пайки в паровой фазе, обеспечивающие применение вакуума для удаления пустот из паяных соединений, проблема образования которых стала особенно актуальной в условиях продолжающегося внедрения бессвинцовых паяльных материалов и расширения номенклатуры ЭК в BGA-корпусах. Также отсутствие пустот важно для мощных сборок, где критичной является хорошая теплопередача от компонентов к плате.
Фактически, данные технологии заключаются в комбинировании тем или иным способом конструкций рабочей камеры оплавления и вакуумной камеры. В горизонтальных системах рабочая камера может одновременно служить вакуумной, для вертикальных систем во многих случаях необходимо создание дополнительного герметичного объема.
Для вертикальной системы процесс пайки в этом случае будет состоять из следующих этапов [9]:
- Загрузка оборудования.
- Транспортировка ПП в зону пайки.
- Обеспечение предварительного нагрева.
- Транспортировка все еще горячей сборки с оплавленным припоем из зоны пайки в вакуумное отделение.
- Закрытие крышки вакуумного отделения.
- Откачка до требуемого уровня вакуума.
- Выдержка при требуемом уровне вакуума.
- Вентиляция вакуумного отделения.
- Открытие крышки вакуумного отделения.
- Транспортировка ПП в зону охлаждения.
- Выгрузка сборки.
Рекомендуемые параметры вакуума [9]: давление 20 – 40 мбар, время откачки до максимального вакуума 7 – 15 сек., время выдержки при максимальном вакууме 3 – 10 сек. Время процесса при этом увеличивается примерно на 25 сек. по сравнению с традиционной технологией с отсутствием вакуума.
Результаты влияния вакуума на устранение пустот приведены на рис. 15 (данные компании rehm Anlagenbau GmbH, площадь контакта паяной поверхности увеличилась при применении вакуума с <68% до >98%) и рис. 16 (данные компании ASSCON Systemtechnik-Elektronik GmbH).
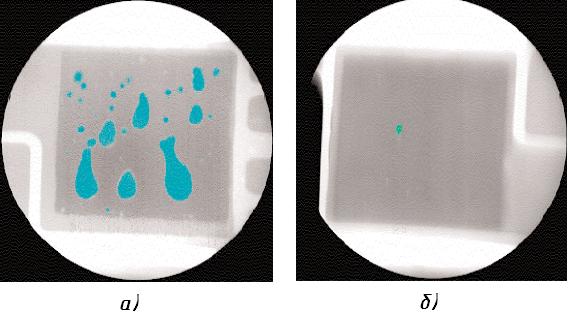
Рис. 15. Результаты традиционного процесса оплавления (а) и процесса с применением вакуума (б). Изображение из [16]
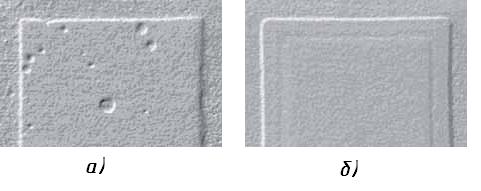
Рис. 16. Результаты традиционного процесса оплавления (а) и процесса с применением вакуума (б). Изображение из [25]
Запатентованная технология компании IBL-Loettechnik GmbH предусматривает создание замкнутого объема непосредственно вокруг сборки сразу же после оплавления припоя (рис. 17). Это устраняет необходимость транспортировки горячей сборки в вакуумное отделение, одновременно сохраняя преимущества вертикальной системы пайки.
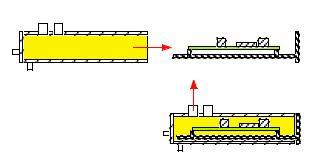
Рис. 17. Комбинация процесса оплавления и вакуумного процесса в одной рабочей камере вертикальной системы. Рисунок из [21]
Заключение
Пайка в паровой фазе переживает в настоящее время период нового подъема. Произведенные усовершенствования традиционной реализации данной технологии позволили преодолеть присущие ей ранее проблемы, связанные прежде всего с резким ростом температуры при нагреве сборки и невозможностью управления этим процессом. Разработаны и продолжают развиваться различные методы исполнения рабочей камеры, осуществления предварительного нагрева, применения вакуума для устранения пустот из паяных соединений. Все это, в сочетании с описанными выше неоспоримыми достоинствами пайки в паровой фазе, обращает на себя внимание технологов и проектировщиков производств, решающих задачи организации новых и усовершенствования существующих участков и линий сборки электронных устройств.
Список использованных источников
- Ray P. Prasad. REFLOW SOLDER PROFILE DEVELOPMENT. www.ecd.com
- apor Phase Reflow for low to medium volume production/APS Novastar LLC. www.novastarinc.com
- Vapor Phase System Intros in North America/Surface Mount Technology (SMT) – 2006. smt.pennnet.com
- John Bashe. A New Approach to Vapor Phase Reflow Soldering/Surface Mount Technology (SMT) – 2006. smt.pennnet.com
- Steve Fraser, Chris Munroe. Lead-free: Using Vapor Phase Reflow in Lead-free Processing/Surface Mount Technology (SMT) – 2005. smt.pennnet.com
- Ray Prasad. Vapor Phase Soldering: The Comeback Kid/Surface Mount Technology (SMT) – 2006. smt.pennnet.com
- Нинг-Ченг-Ли. Технология пайки оплавлением, поиск и устранение дефектов: поверхностный монтаж, BGA, CSP и flip chip технологии. – М.: Издательский Дом «Технологии», 2006.
- Майкл Джюд, Кейт Бриндли. Пайка при сборке электронных модулей. – М.: Издательский Дом «Технологии», 2006.
- Claus Zabel. Vapourphase vacuum-soldering/ASSCON Systemtechnik-Elektronik GmbH. www.atekllc.com
- Saturated vs. Un-Saturated Vapor/ASSCON Systemtechnik-Elektronik GmbH – 2006. www.atekllc.com
- Claus Zabel, Uwe Filor. Secure Lead-Free Processes and Minimize Delta T’s/ ASSCON Systemtechnik-Elektronik GmbH. www.atekllc.com
- VP 2000 Inline Vapor-Phase Soldering System. Technical Data/ASSCON Systemtechnik-Elektronik GmbH. www.atekllc.com (ч.1); www.atekllc.com (ч.2)
- CondensoBatch – The stand-alone condensation system/rehm Anlagenbau GmbH. www.rehm-group.com
- CondensoBatch – The new condensation soldering system/rehm Anlagenbau GmbH. www.rehm-group.com
- CondensoLine – The new inline Condensation Soldering System/rehm Anlagenbau GmbH. www.rehm-group.com
- KLS 400 Batch/Inline/rehm Anlagenbau GmbH. www.rehm-group.com
- Dr. Hans Bell, rehm Anlagenbau GmbH. Blaubeuren in EPP Elektronik Produktion & Prüftechnik – 04/2006, стр. 18.
- Vapour Phase Soldering Based on the IBL Principle/IBL-Loettechnik GmbH. www.ibl-loettechnik.de
- Process description of heat transfer with a condensing vapour phase/IBL-Loettechnik GmbH. www.ibl-loettechnik.de
- Temperature profiles for SnPb solder and lead-free solder/IBL-Loettechnik GmbH. www.ibl-loettechnik.de
- Vac 665. Vacuum Vapour Phase-Reflow Machine for the reduction of voids (patended)/IBL-Loettechnik GmbH. www.ibl-loettechnik.de
- Vapour Phase Soldering Machine LV600/IBL-Loettechnik GmbH. www.ibl-loettechnik.de
- Model RD52 – Vapor Phase REFLOW SYSTEM/R&D Technical Services, Inc. www.rdtechnicalservices.com
- Reflow Comparison Matrix/R&D Technical Services, Inc. www.rdtechnicalservices.com
- VP 6000 Vapour-Phase Vacuum Soldering System/ASSCON Systemtechnik-Elektronik GmbH. www.atekllc.com
|
 |
|