14 августа 2007
Чувствительность электронных компонентов к влажности
Введение
Цель данной статьи – описать характер воздействия влажности на SMT-компоненты в пластиковых и прочих поглощающих влагу корпусах, дать представление об их классификации по уровню чувствительности к влажности, хранению, упаковке и маркировке в соответствии с мировыми стандартами, а также рассмотреть общепринятые рекомендации по подготовке ЭК, подвергшихся воздействию влажности, к пайке оплавлением.
Поддержание целостности корпуса ЭК в течение всего технологического процесса сборки требует принятия ряда специфических мер как поставщиком ЭК, так и компанией-производителем электронных модулей. Эти меры направлены на снижение последствий теплового воздействия на ЭК в процессе их групповой пайки оплавлением. Пластиковые пресс-композиции, применяемые для корпусирования ИС, гигроскопичны и впитывают влагу (рис. 1а). Накопленная влага испаряется в процессе интенсивного нагрева при пайке оплавлением, что вызывает сильное внутреннее давление на различные узлы корпуса, приводящее затем к вздутию, расслоению и, в некоторых случаях, растрескиванию пластикового корпуса ЭК. Трещины могут распространяться как в толще корпуса, так и вдоль выводной рамки (отслоение). Через них к поверхности кристалла ИС могут проникать ионные загрязняющие вещества, вызывающие коррозию и, соответственно, увеличивающие вероятность отказа компонента. Компоненты, внешне не обнаруживающие признаков растрескивания, могут иметь трещины и отслоения внутри корпуса, что влияет как на выход годных изделий, так и на их надежность.
Следует отметить, что чувствительность ЭК к влажности имеет смысл принимать во внимание только при непосредственном температурном воздействии на них, возникающем при пайке оплавлением (конвекционной, инфракрасной или в паровой фазе) и некоторых видах ремонта собранных узлов (с применением горячего «воздушного фена»). Целостность корпусов ЭК не будет нарушена, если они устанавливаются в разъемы. То же самое относится к THT-компонентам, не подвергающимся воздействию среды печи оплавления (т.е. паяемым волной или ручными методами, когда нагрев избирательно прикладывается к выводам ЭК). В случае пайки THT-ЭК волной, их естественной защитой от нагрева служит ПП. Как правило, корпуса ЭК на таких операциях поглощают гораздо меньше тепловой энергии, чем при пайке оплавлением или ремонте, и в предварительных процедурах по устранению из них влаги нет необходимости. SMT-компоненты в герметичных корпусах нечувствительны к действию влаги и не требуют специальных процедур при обращении с ними. Не принимаются во внимание также техпроцессы, предусматривающие погружение корпуса в расплавленный припой (например, пайка волной SMT-компонентов, расположенных на нижней стороне ПП). Однако, в случае, когда THT-компоненты подвергаются воздействию нагретой среды, к ним должны быть применены все процедуры по удалению влаги, предусмотренные для SMT-компонентов.
Механизм воздействия влаги на ЭК
Процесс накопления корпусами ЭК влаги, а также ее критический уровень, который может привести к повреждениям и отказам, зависят от различных свойств материала и конструкции корпуса, среди которых можно выделить следующие:
- форма и размеры полупроводникового кристалла;
- материал и технология крепления кристалла к корпусу;
- размер корпуса;
- количество выводов корпуса;
- толщина слоя герметизирующего материала;
- предел текучести герметизирующего материала;
- показатели диффузии влаги в герметизирующий материал;
- силы адгезии материалов корпуса;
- ТКР материалов корпуса.
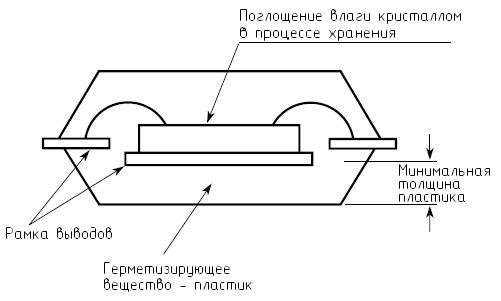
а)
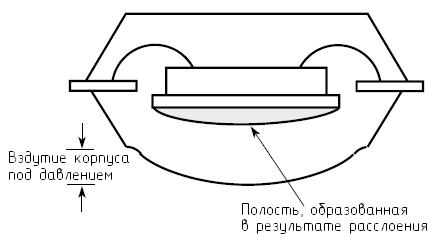
б)
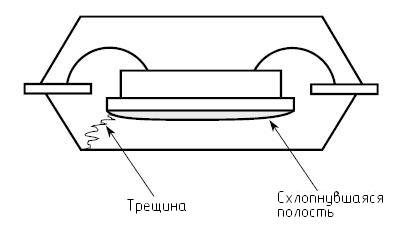
в)
Рис. 1. Механизм образования трещин в пластиковом корпусе: а) накопление корпусом влаги; б) испарение влаги в процессе нагрева; в) образование трещины в корпусе. Рисунок из [6]
Основные причины проникновения влаги внутрь пластикового корпуса ЭК связаны с различными процессами расслоения материалов, включая отделение проволочных соединений корпуса от КП, уменьшение площади поперечного сечения проволочных соединений (утонение), отслоение кристалла от площадки для монтажа и растрескивание тонких пленок на его поверхности, эффект образования «кратеров» в местах крепления проволочных выводов к КП и пр. Степень насыщения корпуса влагой определяется относительной влажностью воздуха, температурой и временем его хранения, а также равновесной растворимостью влаги в материале корпуса – пластике. Появление видимых трещин на поверхности корпуса обычно рассматривается как наиболее наглядное и серьезное последствие накопления влаги. Тем не менее, необходимо помнить, что даже при отсутствии видимых повреждений корпуса, внутри него могут происходить процессы растрескивания/отслоения материалов.
Механизм образования трещин в корпусе представлен на рис. 1. Суммарное воздействие давления водяного пара и термического расширения пластика при нагреве превосходит силу адгезии пластика к площадке для монтажа кристалла. Пластик отслаивается от площадки, образуется полость, заполненная паром, она расширяется, и на корпусе образуется характерное вздутие (рис. 1б). Далее в корпусе появляется трещина, вздутие схлопывается, и пар выходит из полости наружу (рис. 1в). Данный процесс часто называют «эффектом попкорна» за характерный звук, раздающийся при схлопывании полости.Оставшийся объем полости является концентратором напряжений, ведущих к дальнейшему разрастанию трещины при последующих температурных циклах.
Дополнительные причины отказов ЭК
Быстрый нагрев и охлаждение вызывают термический шок ЭК. Различие температур между поверхностью корпуса, где она выше, и его внутренностью вызывает в корпусе термомеханические напряжения. Степень термического шока выше при пайке в паровой фазе, чем при конвекционной и инфракрасной. Профиль оплавления для ИК-пайки обычно предусматривает нагрев ЭК со скоростью 2 – 6°С/сек., для конвекционной – менее 2°С/сек. В процессе пайки в паровой фазе возможно обеспечить только ограниченный контроль скорости нагрева ЭК и ПП. Максимальная скорость нагрева в процессе такой пайки гораздо выше (до 25°С/сек.) Такая быстрая скорость подъема температуры может вызвать повреждение ЭК вследствие разницы в ТКР различных материалов корпуса. Эта проблема еще более усиливается в случае накопления ЭК избыточной влаги.
Флюсы, входящие в состав паяльных паст, являются главными поставщиками ионных загрязнений, которые могут привести к коррозии слоя металлизации кристалла ИС в случае транспортировки загрязнений к поверхности кристалла. Следует избегать флюсов, содержащих соляную кислоту и другие галоидные соединения, а также высокоактивных флюсов, (на основе органических кислот). Где возможно, следует использовать RMA-флюсы и флюсы с низкой активностью (NC и пр.)
Основываясь на рекомендациях [6], ЭК с медными выводами, покрытыми сплавом олово-свинец, необходимо выдерживать при 125°С не более 48 часов, чтобы выводы не потеряли гарантию пайки вследствие окисления и/или роста интерметаллических соединений. Согласно стандарту [2], суммарное время сушки при температурах 90 – 125°С не должно превышать 96 часов. Сушка при температурах выше 125°С недопустима без консультации с поставщиком ЭК.
С целью недопущения обрыва выводов и разрушения паяных соединений внутри корпуса, при проведении ультразвуковой очистки собранных узлов необходимо придерживаться следующих режимов: диапазон частот ультразвука – от 39 до 66 кГц; время очистки – 3 мин. на цикл для 5 циклов очистки, суммарное время не должно быть больше 15 мин [6].
Необходимое оборудование
Для проведения тестов на принадлежность ЭК к тому или иному уровню чувствительности к влажности необходима камера для климатических испытаний с возможностью обеспечения следующих режимов температуры/относительной влажности воздуха: 85°C/85%, 85°C/60%, 60°C/60%, 30°C/60% при колебаниях ± 2°C/± 3%, а также конвекционная печь для проведения тестовой пайки оплавлением.
Для хранения ЭК, предварительной сушки ЭК перед упаковкой в защитный пакет либо окончательной сушки перед пайкой оплавлением требуется шкаф сухого хранения, а также вентилируемая печь с режимами нагрева до 125°C, 90°C и 40°C +5/-0 °C.
Уровни чувствительности ЭК к влажности
По уровню чувствительности к влажности (Moisture Sensitivity Level, MSL) ЭК подразделяются на 6 уровней согласно стандарту [1]. Процедура определения принадлежности ЭК к определенному уровню включает в себя следующие этапы:
- начальная инспекция образцов ЭК на предмет наличия трещин/отслоений (визуальная и с применением акустического микроскопа);
- предварительная сушка ЭК в течение 24 часов при температуре 125 +5/-0°C для получения полностью «сухого» состояния корпусов;
- помещение ЭК в сухой, чистый, неглубокий контейнер и сушка их в климатической камере согласно режимам, приведенным в таблица 1 для данного уровня MSL (начиная с 1-го);
- проведение для ЭК после сушки в климатической камере (не ранее, чем через 15 мин. и не позднее, чем через 4 часа после вынимания их из нее), троекратных циклов пайки оплавления по стандартному профилю, указанному в [1] (выдержка между циклами – минимум 5 и максимум 60 мин.);
- окончательная инспекция ЭК на предмет внешних трещин (оптический микроскоп с увеличением 40x), проведение электрических тестов согласно спецификациям производителей ЭК, анализ внутренних дефектов с помощью сканирующего акустического микроскопа.
Критерии отказов ЭК при этом следующие:
- Видимая с помощью оптического микроскопа с увеличением 40x трещина.
- Отказ по результатам электрических тестов.
- Внутренняя трещина, пересекающая проволочное, шариковое либо сварное соединение.
- Внутренняя трещина, распространяющаяся от вывода к любому другому внутреннему элементу корпуса (выводу, кристаллу, площадке для монтажа кристалла).
- Внутренняя трещина, распространяющаяся на более чем 2/3 расстояния от любого внутреннего элемента корпуса до внешней его границы.
- Изменения плоскостности корпуса, вызванные деформацией, короблением, вспучиванием, видимые невооруженным глазом.
Если отказал хотя бы один из тестируемых образцов, ЭК считается не прошедшим тест на данном уровне MSL, и исследуется новая группа образцов при режимах, соответствующих следующему уровню чувствительности ЭК к влажности.
Также существует ряд критериев отказа, основанных на качественной и количественной оценке расслоения различных материалов корпуса (в процентах разницы между состояниями после предварительной сушки и после оплавления), различающиеся в зависимости от конструкции корпуса [1]. Тем не менее, если ЭК успешно прошел электрические тесты, но наблюдается отслоение материала на обратной стороне площадки для монтажа кристалла, элементе-распределителе теплоты, обратной стороне кристалла, но при этом нет внешних признаков наличия трещин и других расслоений, и корпус удовлетворяет требованиям п. 6, он считается прошедшим тест на данный уровень MSL. Для оценки влияния расслоения на надежность ЭК могут потребоваться исследования согласно [4], а также методикам производителя ЭК.
Таблица 1. Уровни чувствительности ЭК к влажности (MSL) по стандарту IPC/JEDEC J-STD-020C
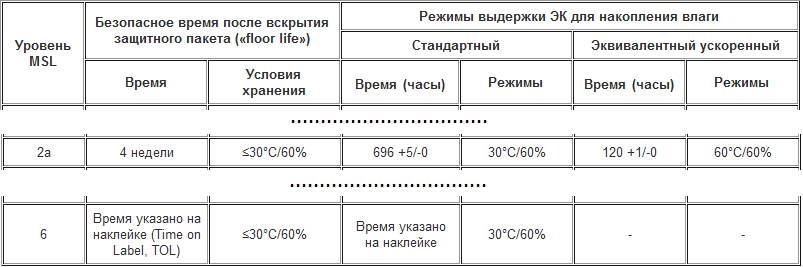
Требования к упаковке ЭК перед поставкой
Защитная упаковка ЭК обеспечивается дистрибьютором и, как правило, требует наличия следующих материалов:
- упакованных ЭК в трубчатых кассетах, бобинах с лентой, матричных поддонах;
- влагопоглотителя;
- специального пакета с защитой от влажности;
- наклеек, предупреждающих о наличии чувствительного к влажности содержимого;
- карточки-индикатора влажности.
ЭК поставляются от дистрибьютора в т.н. «сухих» упаковках (dry pack), которые представляют собой герметично закрытый пакет с защитой от влажности (Moisture Barrier Bag, MBB, рис. 2) с находящимися внутри носителями с ЭК, влагопоглотителем и карточкой-индикатором влажности (Humidity Indicator Card, HIC). Основными требованиями к защитному пакету (стандарт MIL-PRF-81705, Тип I) являются гибкость, защита от статического электричества, механическая прочность, стойкость к проколам, возможность термосклеивания. Скорость проникновения водяных паров должна быть Ј0,002 гЧм/100 кв.дюймов за 24 часа при 40°С. При запечатывании пакета посредством термосклеивания допускается небольшое снижение внутреннего давления воздуха.
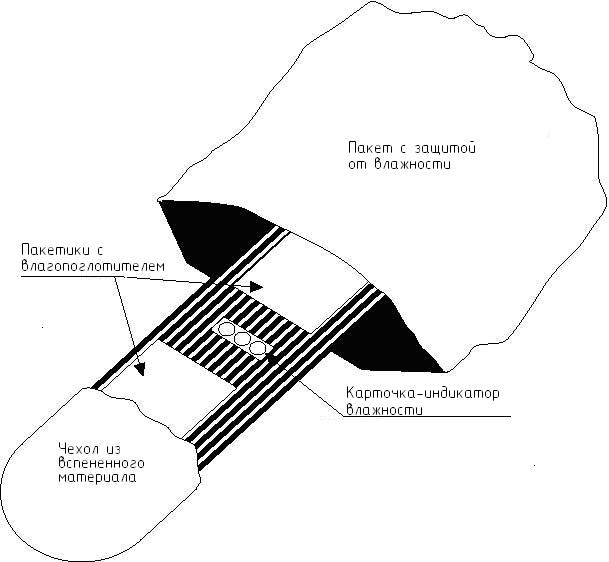
Рис. 2. Состав пакета с защитой от влажности. (Рисунок JEDEC)
Влагопоглотитель (стандарт MIL-D-3464, Тип II) должен быть некоррозионным, не образовывать пыли, быть упакованным во влагопроницаемый пакетик и обладать требуемыми абсорбирующими свойствами. Количество влагопоглотителя должно обеспечивать внутри упаковки с ЭК относительную влажность менее 10% при 25°С. Формулы для расчета необходимого количества влагопоглотителя приведены в [2].
Карточка-индикатор влажности, как правило, представляет собой карточку из впитывающей влагу бумаги, снабженную тремя цветными кружками – индикаторами уровней относительной влажности в 5, 10 и 60%. Внешний вид карточки представлен на рис. 3. Об уровне влажности судят по изменению цветов соответствующих кружков согласно таблице 2. Могут быть использованы другие цветовые схемы. Карточка сохраняет достоверность показаний в закрытом пакете до 5 лет.
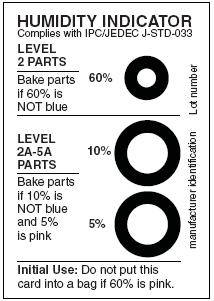
Рис. 3. Внешний вид карточки-индикатора влажности. (Рисунок JEDEC)
Таблица 2. Расшифровка показаний карточки-индикатора влажности по стандарту IPC/JEDEC J-STD-033B.1
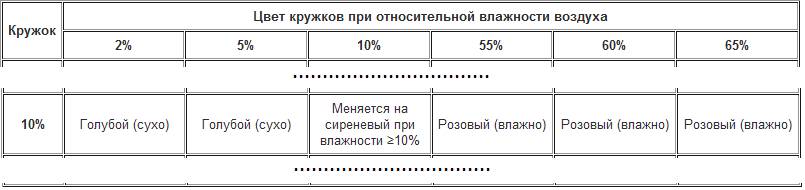
Избыточная влажность, о которой сигнализирует карточка, может являться следствием неправильной комплектации защитного пакета (например, отсутствующий либо неправильно подобранный влагопоглотитель), неправильного обращения, приведшего к проколам или разрывам пакета, а также хранением в неподходящих условиях. В стандартах описаны следующие варианты индикации:
- Если все три кружка показывают «сухо», ЭК уровней MSL 2 – 5а сухие в достаточной степени.
- Если кружок 5% показывает «влажно», 10% НЕ показывает «сухо», а 60% показывает «сухо», ЭК уровня MSL 2 сухие в достаточной степени, ЭК уровней MSL 2а – 5а накопили избыточное количество влаги и требуют сушки.
- Если все три кружка показывают «влажно», ЭК уровня MSL 2 накопили избыточное количество влаги и требуют сушки.
Если перед запечатыванием пакета кружок 60% показывает «влажно», карточка должна быть забракована.
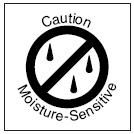
Рис. 4. Наклейка-идентификатор чувствительного к влажности содержимого на защитный пакет. (Рисунок JEDEC)
На защитный пакет наносятся, как правило, две характерные наклейки: идентификатор чувствительного к влажности содержимого (Moisture-Sensitive Identification Label, MSID, рис. 4) и предупреждающая наклейка (Caution Label, рис. 5), выполненные согласно стандарту EIA/JEDEC JEP113-B [3].
Наклейка для ЭК уровня MSL 1 носит информационный характер (рис. 5а), сообщает об уровне MSL = 1 (квадрат с подписью «level»), отсутствии чувствительности данных ЭК к влажности при соблюдении условий хранения ≤30°C/85% и максимальной температуре корпуса при оплавлении не более 235°C. Наносится на транспортную тару низшего уровня в случае, если температура оплавления ЭК отличается от 220–225°C.
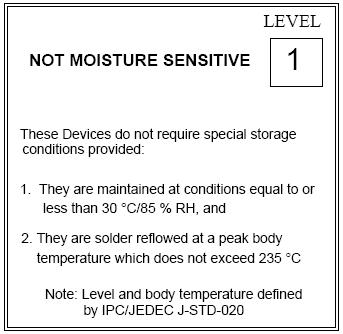
а)
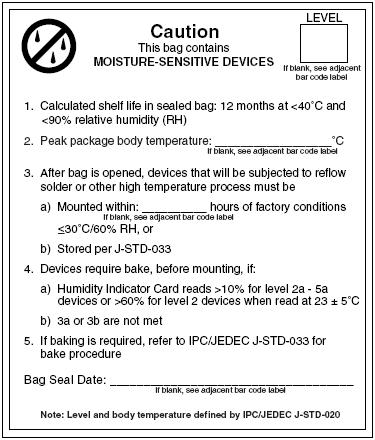
б)
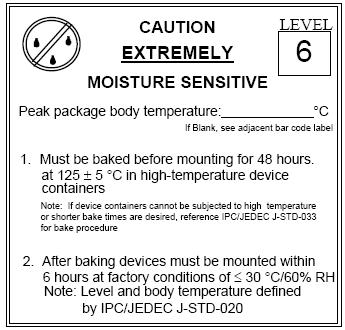
в)
Рис. 5. Предупреждающая наклейка на защитный пакет: а) для уровня MSL 1; б) для уровней MSL 2-5; в) для уровня MSL 6. (Рисунок JEDEC)
На предупреждающую наклейку для уровней MSL 2–5 наносятся следующие надписи (рис. 5б):
- Уровень MSL (квадрат с подписью «level»).
- Время безопасного хранения в защитном пакете («calculated shelf life»).
- Максимальная температура корпуса («peak package body temperature»).
- Безопасный интервал времени между выниманием ЭК из защитного пакета и пайкой при 30°C/60% («floor life»).
- Время герметичного запечатывания пакета («bag seal date») в формате “MMDDYY”, “YYWW” или эквивалентном.
ЭК уровня MSL 6 являются экстремально чувствительными к влажности и не требуют «сухой» упаковки, так как в любом случае подлежат обязательной сушке перед пайкой. Тем не менее, такая упаковка является «символом» чувствительных к влажности ЭК и рекомендуется к применению в данном случае, даже без влагопоглотителя и карточки-индикатора внутри запечатанного пакета. На наклейке обозначаются (рис. 5в):
- Уровень MSL = 6 (квадрат с подписью «level»);
- Максимальная температура корпуса («peak package body temperature»);
- Указания к обязательной сушке ЭК в течение 48 часов при температуре 125±5°C в высокотемпературной упаковке, а также монтажу в течение последующих 6 часов при 30°C/60%.
Информация предупреждающей наклейки может дублироваться на этикетке со штриховым кодом (рис. 6), где указывается время запечатывания пакета («bag seal date»), уровень MSL («Level») и время «floor life» («hours»), которая прикрепляется к защитному пакету.
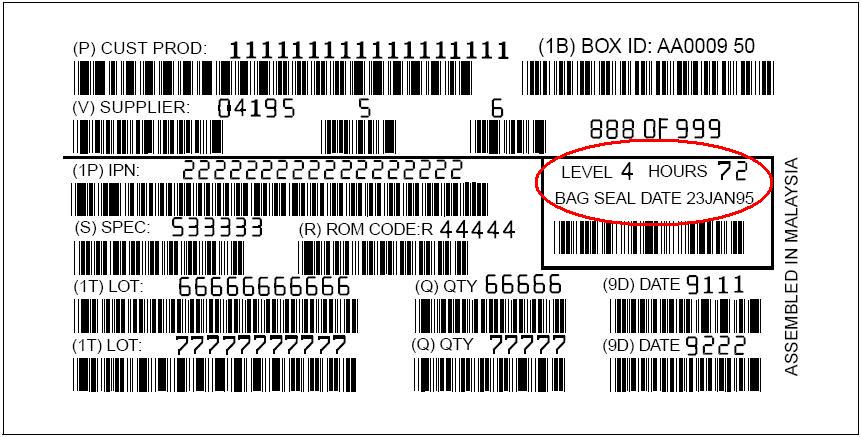
Рис. 6. Этикетка со штриховым кодом на защитный пакет. Рисунок из [6]
Пример суммарных требований к упаковке согласно уровням MSL приведен в таблице 3.
Таблица 3. Требования к упаковке ЭК по стандарту IPC/JEDEC J-STD-033B
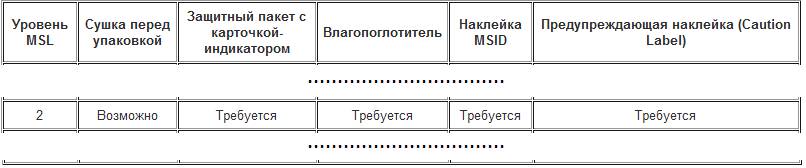
Герметизация пакета производится специальным устройством-вакуумизатором, при помощи которого производится герметичное термосклеивание пакета, находящегося внутри вакуумной камеры.
Типичная последовательность операций при этом следующая:
- положить носитель с ЭК и все необходимые принадлежности (влагопоглотитель, карточку-индикатор) в пакет;
- используя большие пальцы обеих рук, сделать кладки на боковых сторонах пакета для возможности правильного оттока воздуха;
- вставить пакет между зажимными губками вакуумизатора, проверив, чтобы внутри вакуумной камеры устройства оставался открытый конец пакета длиной около 10 мм;
- держа пакет одной рукой, второй нажать на верхнюю зажимную губку до ее блокировки электромагнитом, после чего начнется цикл откачки, создаваемый в процессе которого вакуум в ряде моделей можно отслеживать по встроенному вакуумметру;
- после достижения необходимого вакуума нажать на кнопку, запускающую процесс термосклеивания.
Времена откачки и склеивания настраиваются. Ряд вакуумизаторов имеют дополнительную возможность заполнения пакета инертным газом.
Предварительная сушка ЭК перед упаковкой в защитный пакет
ЭК, относящиеся к уровням 2а – 5а, перед упаковкой в защитный пакет должны быть просушены. Время между сушкой и упаковкой не должно превышать времени MET за вычетом времени, затраченного дистрибьютором на переупаковку ЭК. Если ЭК переупаковываются с активным влагопоглотителем, это время не должно вычитаться из времени MET. В случае, когда время между сушкой и упаковкой оказалось больше допустимого, ЭК должны подвергнуться дополнительной сушке (см. п.п. «Сушка перед пайкой оплавлением»).
Необходимо учитывать, что носители ЭК (ленты, трубчатые кассеты, поддоны) также могут накапливать влагу, поэтому они также должны быть просушены, либо в защитный пакет добавлен дополнительный объем влагопоглотителя.
В таблице 4 приведен пример режимов сушки изначально сухих ЭК, далее подвергшихся действию окружающей среды с относительной влажностью ≤ 60%, перед упаковкой в защитный пакет на предприятии-изготовителе либо у дистрибьютора при максимальном времени MET, равном 24 часам. Если время воздействия среды при 30°С/60% было кратким, достаточной является сушка при комнатной температуре с использованием «сухой» упаковки или шкафа сухого хранения. Если прошло не более 30 мин., может использоваться исходный влагопоглотитель.
Таблица 4. Режимы сушки ЭК перед упаковкой в защитный пакет по стандарту IPC/JEDEC J-STD-033B.1
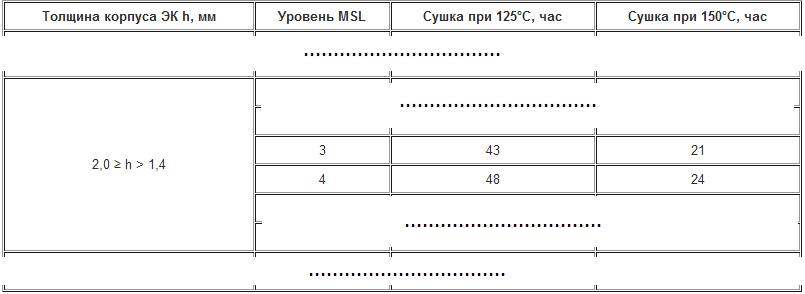
Безопасное время хранения ЭК в запечатанном виде без превышения норм относительной влажности внутренней среды пакета (т.н. «shelf life») должно быть не меньше 12 месяцев, начиная с даты запечатывания пакета, при его хранении в неконденсирующейся среде при условиях Ј40°С/90%. В случае проведения сушки ЭК и запечатывания их в пакет со свежим влагопоглотителем, время хранения обнуляется.
Сушка перед пайкой оплавлением
После поставки в защитном пакете от дистрибьютора на предприятие, осуществляющее сборку электронных модулей, ЭК также требуют определенных процедур по их хранению, обращению с ними и, возможно, удалению избыточной влажности.
Важным параметром хранения чувствительных к влажности ЭК является допустимый период времени между выниманием их из защитного пакета, шкафа сухого хранения либо окончанием сушки и процессом пайки оплавлением (т.н. «floor life»). Если это время оказалось превышенным, необходима дополнительная сушка ЭК перед пайкой. Пример режимов проведения такой сушки приведен в таблице 5.
Таблица 5. Нормальные режимы сушки установленных либо не установленных на ПП ЭК перед пайкой оплавлением согласно стандарту IPC/JEDEC J-STD-033B.1

Пример условий остановки или обнуления времени «floor life» приведен в таблице 6. Время «floor life» начинает новый отсчет с 0 после проведения сушки/выдержки согласно данным таблицы.
Таблица 6. Условия остановки или обнуления времени «floor life» на территории компании-сборщика согласно стандарту IPC/JEDEC J-STD-033B.1
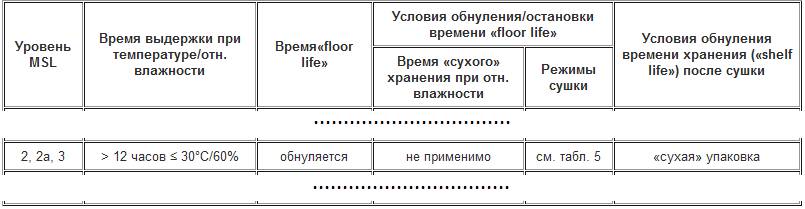
Если условия окружающей среды на производстве отличаются от указанных в столбце «Условия хранения» таблицы 1, значения времени «floor life» для ЭК различных уровней MSL должны быть скорректированы. Стандарт JESD22-A120 [5], основываясь на знании диффундирующей способности влаги в материалы корпусов ЭК, предлагает сводную таблицу скорректированных времен «floor life» для относительной влажности воздуха 5 – 90% и температур 20, 25, 30 и 35°С при различных толщинах корпуса ЭК (таблица 7). Данная таблица справедлива для корпусов ЭК, прессованных из новолака, бифенила или многофункциональных эпоксидных пресс-компаундов.
Таблица 7. Рекомендованные эквивалентные времена «floor life» (дн.) в зависимости от условий окружающей среды, отличающихся от стандартных, согласно IPC/JEDEC J-STD-033B.1
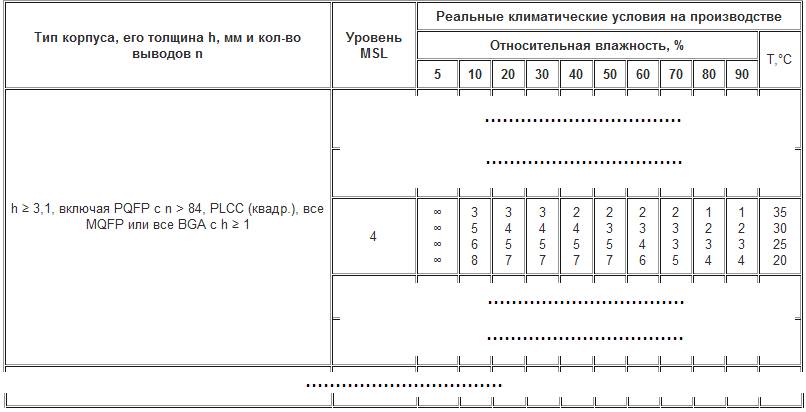
Если производителем ЭК не указано обратное, SMD-компоненты поставляются в групповых упаковках, допускающих температурное воздействие на них в пределах 125°С. Если упаковка ЭК не предназначена для воздействия высоких температур (более 40°С), перед сушкой их необходимо вынуть из упаковки, переложить в высокотемпературную тару, просушить и вернуть обратно в низкотемпературную упаковку.
Обращение с ЭК после вскрытия защитного пакета
После получения защитного пакета с ЭК определяется оставшееся время хранения согласно дате запечатывания пакета («shelf life» – по этикетке со штриховым кодом либо предупреждающей наклейке). Пакет осматривается на предмет отсутствия проколов, разрывов и прочих повреждений содержимого либо внутреннего слоя многослойного пакета. Если найдены повреждения, и карточка-индикатор показывает максимальный достигнутый уровень влажности, необходима сушка ЭК в течение 48 часов при 125°С или согласно режимам из таблицы 5.
Если время безопасного хранения пакета истекло (срок хранения превышает 12 месяцев со дня запечатывания), но карточка-индикатор показывает допустимый уровень влажности, возможна пайка ЭК оплавлением согласно указанному уровню MSL.
Далее пакет вскрывается отрезанием его верхней части у места герметизации. Необходимо производить обрезку так, чтобы оставалась возможность дальнейшего запечатывания пакета (при необходимости промежуточного хранения ЭК).
Если на сборку одновременно поставляются не все ЭК из пакета, оставшиеся могут храниться в условиях, когда время «floor life» остается на нуле. Это может быть шкаф сухого хранения в условиях воздушной или азотной атмосферы (25±5°С), восстанавливающий параметры хранения по влажности в течение 1 часа после открытия/закрытия дверцы. SMD-компоненты без защитного пакета могут храниться в:
- шкафу сухого хранения при влажности 10%; такое хранение не является заменой защитного пакета, время хранения ограничено согласно таблице 7, при превышении для обнуления времени «floor life» требуется сушка согласно режимам из таблицы 4;
- шкафу сухого хранения при влажности 5%; такое хранение может считаться заменой защитного пакета, содержание эквивалентно нахождению в защитном пакете с неограниченным временем хранения (время «shelf life» остается на нуле).
В случае превышения указанной на предупреждающей наклейке температуры оплавления могут потребоваться дополнительные меры по удалению влаги из корпуса ЭК, выходящие за рамки описываемых процедур. В этом случае необходима консультация с поставщиком ЭК.
В случае многократных циклов пайки одной ПП необходимо удостовериться, что время «floor life» не истекло вплоть до начала последнего цикла оплавления. В противном случае необходима предварительная сушка платы с установленными ЭК. Максимально допускается прохождение одним и тем же ЭК трех циклов оплавления. Отмывка ПП с корпусами, имеющими полости, может привести к дополнительному накоплению влаги в них, что должно быть также принято во внимание.
Следует помнить, что время «floor life» НЕ обнуляется любым процессом пайки/ремонта ПП.
Если ЭК должен быть выпаян из сборки, рекомендуется использование локального нагрева с тем, чтобы температура любого ЭК на ПП не превышала 200°С. Это минимизирует негативные последствия, связанные с накоплением влаги ЭК. Если температура любого ЭК при процессе ремонта превышает 200°С, сборка должна быть предварительно просушена. Температура ЭК измеряется в центре верхней части корпуса. Все ЭК, чье время floor life» не превышает допустимого согласно уровню MSL, может подвергаться воздействию своей максимальной температуры оплавления согласно [1].
Для просушки собранных изделий на ПП обычно применяется температура 125°С, за исключением случаев, когда на ПП наличествуют ЭК, для которых такая температура недопустима (например, органические светодиоды, батареи, электролитические конденсаторы). С учетом этого режимы сушки выбираются из таблицы 5.
Заключение
Несмотря на кажущуюся малозначительность, проникновение влаги в пластиковые корпуса ЭК оборачивается серьезными проблемами при сборке. Необходимо уделять повышенное внимание состоянию ЭК и условиям их хранения на всем этапе движения от производителя ЭК к печи оплавления. Описанные в данной статье процедуры помогут избежать производственных дефектов, связанных с накоплением ЭК избыточной влажности, увеличат выход годных и эксплуатационную надежность собираемых электронных модулей.
Список использованных источников
- IPC/JEDEC. J-STD-020C. Moisture/Reflow Sensitivity Classification for Non-hermetic Solid State Surface Mount Devices. Generic Standard on Printed Board Design/JEDEC, 2004 – 13 p. www.jedec.org
- IPC/JEDEC. J-STD-033B.1. Handling, Packing, Shipping and Use of Moisture/Reflow Sensitive Surface Mount Devices/JEDEC, 2007 – 26 p. www.jedec.org
- EIA/JEDEC. JEP113-B. Symbol and Labels for Moisture-Sensitive Devices/EIA/JEDEC, 1999 – 10 p. www.jedec.org
- JEDEC. JESD22-A113E. Preconditioning of Nonhermetic Surface Mount Devices Prior to Reliability Testing/JEDEC, 2006 – 16 p. www.jedec.org
- JEDEC. JESD22-A120. Test Method for the Measurement of Moisture Diffusivity and Water Solubility in Organic Materials Used in Integrated Circuits/JEDEC, 2001 – 13 p. www.jedec.org
- Intel Packaging Databook. Chapter 8. Moisture Sensitivity/Desiccant Packaging/Handling of PSMCs/Intel Corp., 2000 – 27 p. www.intel.com
- Texas Instruments. Application Report SZZA021C. Semiconductor Packing Methodology/Cles Troxtell, Bobby O’Donley, Ray Purdom, Edgar Zuniga/TI, 2005 – 29 p. www.ti.com
|